The life expectancy or durability of the D1P Series pumps can vary based on several factors:
- Operating Conditions: The pump’s lifespan can be influenced by the operating environment, such as temperature, pressure, and the presence of contaminants. Pumps operating in harsh conditions might have a different lifespan compared to those in controlled environments.
- Maintenance: Regular and proper maintenance significantly impacts the longevity of the pumps. Following manufacturer-recommended maintenance schedules, fluid checks, and component inspections can prolong the pump’s lifespan.
- Load and Usage: The workload and frequency of use also affect the pump’s durability. Pumps subjected to heavy-duty continuous operation might have a different lifespan compared to those used intermittently or under lighter loads.
- Quality of Components: The quality of materials used in the pump’s construction, including seals, bearings, and internal components, plays a vital role in determining its durability.
- Manufacturer Specifications: Manufacturers often provide estimated service life or durability guidelines based on design, materials, and intended usage. These specifications can give an idea of the expected lifespan under optimal conditions.
Generally, with proper care and maintenance, the D1P Series pumps can have a relatively long service life, often lasting several years in industrial applications. However, the specific lifespan can vary widely based on the factors mentioned above and the actual conditions in which the pump operates. Adhering to recommended maintenance practices and operating within specified parameters can help maximize the pump’s durability and service life. Consulting the manufacturer’s documentation or contacting their support can provide more precise information regarding the expected lifespan of the D1P Series pumps.
What are the key materials used in manufacturing the D1P series pumps?
The key materials used in manufacturing the D1P Series pumps typically include high-grade materials chosen for their durability, resistance to wear, and suitability for hydraulic applications. China D1P Series Pump While specific material compositions may vary based on the pump’s components and manufacturer specifications, common materials used in these pumps might include:
- Steel Alloys: Components like pump housings, shafts, and gears are often made from high-strength steel alloys. These alloys provide durability and resistance to wear under high-pressure conditions.
- Aluminum Alloys: Certain pump components, such as casing covers or lightweight parts, might be crafted from aluminum alloys for their lightweight properties and corrosion resistance.
- Cast Iron: Some internal components, such as pistons or valve plates, may be made from cast iron for its strength and resistance to abrasion.
- Bronze or Brass: Bearings or bushings within the pump might utilize bronze or brass for their lubricating properties and ability to withstand friction.
- Sealing Materials: Seals and gaskets within the pump often use elastomers or synthetic materials designed to withstand hydraulic fluids, pressure, and temperature variations.
- Ceramic or Hardened Coatings: Certain high-wear areas or critical surfaces might feature ceramic coatings or hardened layers to enhance durability and reduce friction.
- Plastics or Polymers: Some non-load-bearing or low-friction components might incorporate plastic or polymer materials for their corrosion resistance and ability to reduce friction.
The specific choice of materials for different components within the D1P Series pumps is determined by factors such as the intended application, hydraulic fluid compatibility, pressure requirements, and the need for durability and reliability in diverse operating conditions. Manufacturers often optimize material selections to ensure optimal performance, longevity, and reliability of these pumps.
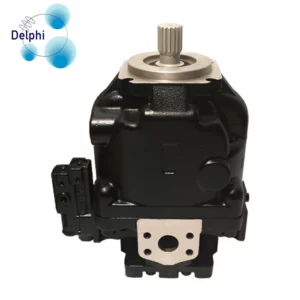